SUPPLY CHAIN RISK
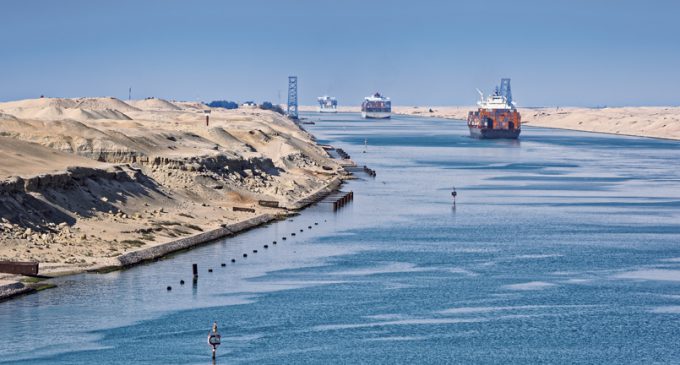
Risk Management
By Randy Boss, CRM, MWCA, SHRM-SCP
SUPPLY CHAIN RISK
Things to consider when creating a strategy to manage disruptions
On March 23 of this year, a 1,300-foot, 220,000-ton container ship got stuck in the Suez Canal, blocking traffic for nearly a week before it was finally freed. Picture trying to make a three-point turn in your eight-foot car on a six-foot wide street. Nothing good can happen.
For those who are Wikipedia-challenged, the Suez Canal is a human-made waterway that cuts across the Isthmus of Suez in Egypt. It connects the Mediterranean Sea to the Red Sea, making it the shortest maritime route between Asia and Europe. It has become one of the world’s most heavily used shipping lanes since it was constructed in 1869. The Suez Canal is essential because it offers a direct route between the North Atlantic and Indian Oceans. Without it, ships need to go around the horn of Africa, adding 5,000 miles and five days to their trip. Not to mention tremendous added costs.
[W]hen the ship Ever Given … got stuck, it prevented I00 ships a day from passing through, holding up about I2% of global trade … .
So, when the ship Ever Given, owned by container transportation and shipping company Evergreen Marine, got stuck, it prevented 100 ships a day from passing through, holding up about 12% of global trade, around one million barrels of oil and roughly 8% of liquefied natural gas. Experts estimate the canal’s revenues were taking a $14 million to $15 million hit for each day of the blockage.
So how does a 120-mile-long canal over 6,000 miles from the United States affect business owners we work with every day? Here’s an example: I was recently talking with a contractor who installs gutters on homes. He said his supplier of screws called and informed him they could not deliver this essential product because of the Suez Canal blockage. Fortunately, he was able to find another supplier to get him through, but it did make him pause and create a plan to keep a higher inventory on hand to avoid this in the future.
As bad as it seems, the Suez Canal has seen worse blockages—some of which lasted for years. According to the Suez Canal Authority, which maintains and operates the waterway, the Suez Canal has closed five times since it opened for navigation in 1869. For example, following the Six-Day War of 1967, Egypt closed the Canal to international shipping as Israeli forces struck again at the Canal Zone and entrenched in the Sinai Peninsula. Fifteen cargo ships became trapped and remained in the canal until 1975, eight years later.
Aside from waterway blockages, there are other types of supply chain disruptions to consider, such as pandemics, natural disasters, transportation failures and delays, product problems, price fluctuations, and cyber attacks, to mention a few.
The COVID-19 pandemic highlighted that more than 200 of the Fortune Global 500 firms have a presence in Wuhan, the highly industrialized province where the outbreak originated and which was hardest hit. Companies whose supply chain relies on Tier 1 (direct) or Tier 2 (secondary) suppliers experienced significant disruption. And even a year after the pandemic hit the United States, today the business collateral damage is still being felt by companies relying on a ravaged India as part of its supply chain.
Many companies use a just-in-time (JIT) method that relies on a predictable supply chain. A just-in-time supply chain moves material just before it’s needed in the manufacturing process. The method reduces the need to warehouse excessive materials, and it works best when each operation is closely synchronized with the subsequent operations.
But if this supply chain is disrupted, the supplier can’t meet their customers’ JIT requirements; they risk losing accounts and revenue. If the original equipment manufacturer fails to get the parts needed to support their manufacturing efforts, they can’t produce and deliver their products to customers on time, thus risking losing their customer base.
Supply chain cybersecurity threats are designed to disrupt the various processes involved in the development of goods. According to the National Institute of Standards and Technology, supply chain cybersecurity threats can touch virtually every production and delivery element at once, including design, fabrication, output, transportation, delivery, and more. They can also involve the theft of intellectual property targeting a particular commodity.
Here are a few things to consider while creating a strategy for managing supply chain disruptions:
- Create a supply chain emergency plan
- Build up inventory
- Conduct a supply chain vulnerability audit
- Identify backup suppliers
- Diversify supply base
- Partner with a logistics expert
- Adopt risk evaluation tools
What supply chain risks keep your clients awake at night? While large companies with robust enterprise risk management systems assess and attempt to mitigate supply chain risk, many middle market-sized businesses haven’t even thought about it until they are affected directly.
As a risk advisor, a conversation with clients about managing their enterprise supply chain risk, along with business continuity, will be appreciated.
The author
Randy Boss is a Certified Risk Manager at Ottawa Kent in Jenison, Michigan. As a risk manager, he designs, builds and implements risk management and insurance plans for middle market companies in the areas of safety, work comp, human resources, property/casualty and benefits. He has over 40 years’ experience and has been at Ottawa Kent for 39 years. He is the co-founder of emergeapps.com, web apps for insurance agents to share with employers. Randy can be reached at rboss@ottawakent.com.